- Home
- Transportation
- We Always Wondered How Subway Cars Are Built, So We Went To Yonkers To Find Out
We Always Wondered How Subway Cars Are Built, So We Went To Yonkers To Find Out
Kawasaki has been making heavy rail cars since 1906. Their Yonkers factory recently celebrated its 25th anniversary. Why Yonkers? Kawasaki's original contract stipulated that subway cars made for the Port Authority of New York must be manufactured within a 25-mile radius of the Statue of Liberty.

Rolling stock makes up 10% of Kawaski's manufacturing, which includes commuter rail, high speed rail, light rail, and heavy rail. At this site, they do final assembly of brand new cars, as well refurbish older ones.
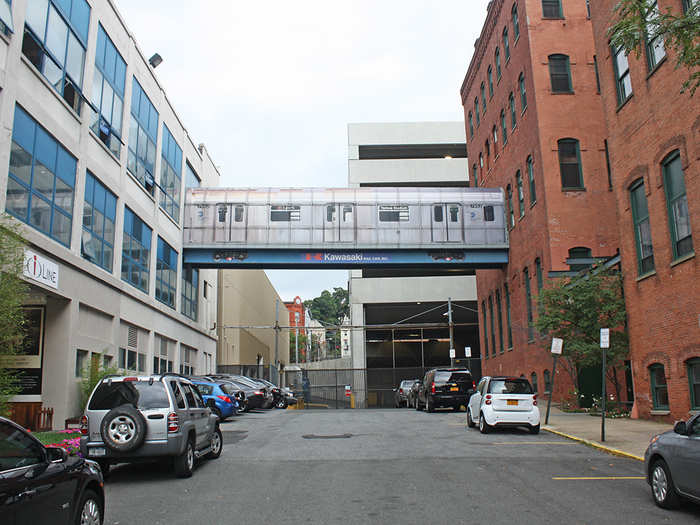
Kawasaki is the second largest manufacturer of train cars, owning 23.5% of the passenger rail market, just behind Bombardier with 30.1%. The third largest competitor is Siemens. Subway cars are built on contract from various authorities. The Yonkers plant has built and overhauled cars for the Port Authority, LIRR, PATH, SEPTA, and others.
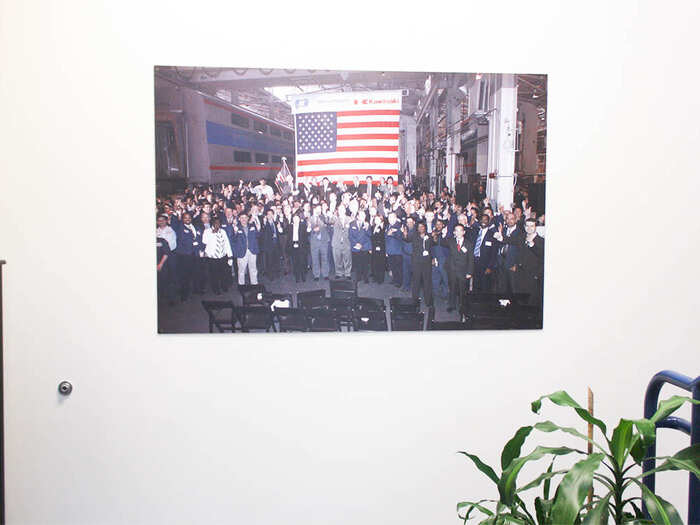
At 150,000 square feet, the factory is huge. Over 4,500 cars have been assembled at the plant.
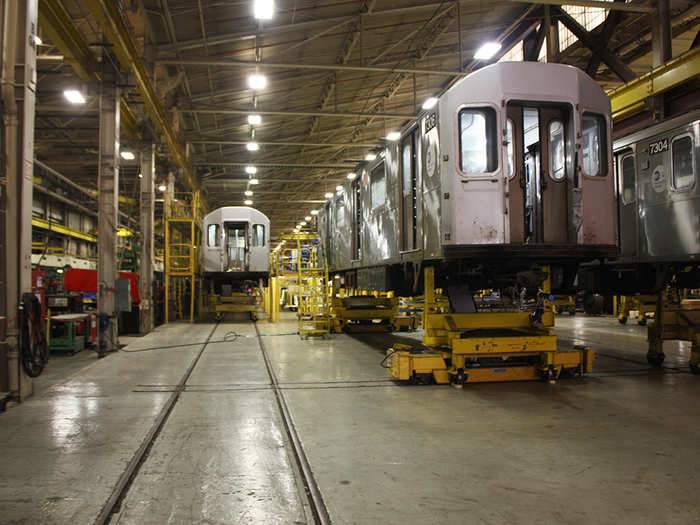
All the parts for the cars are made in-house, using raw materials and man power. Depending on the contract, these parts can include flooring, ceiling panels, wall panels, doors, lighting, seats, wiring, heating, air conditioning, piping, and all underfloor and cab equipment.
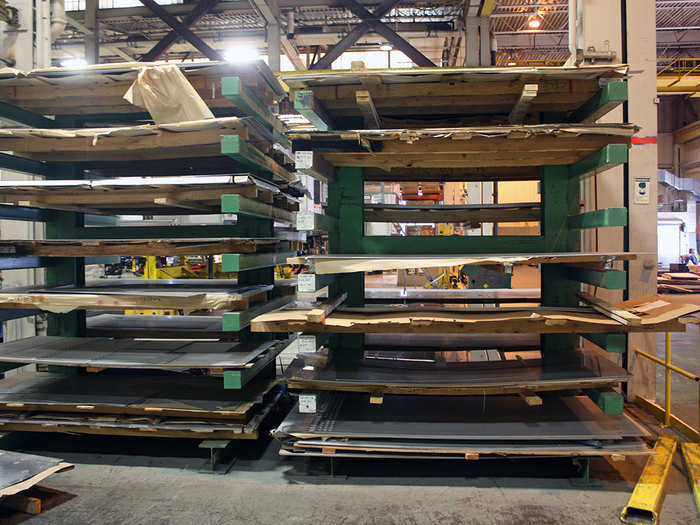
Sheets of stainless steel are cut into shapes using a laser cutter or are punched out via a large machine. They are then bent and formed by machines and by hand into fixtures for the subway cars.
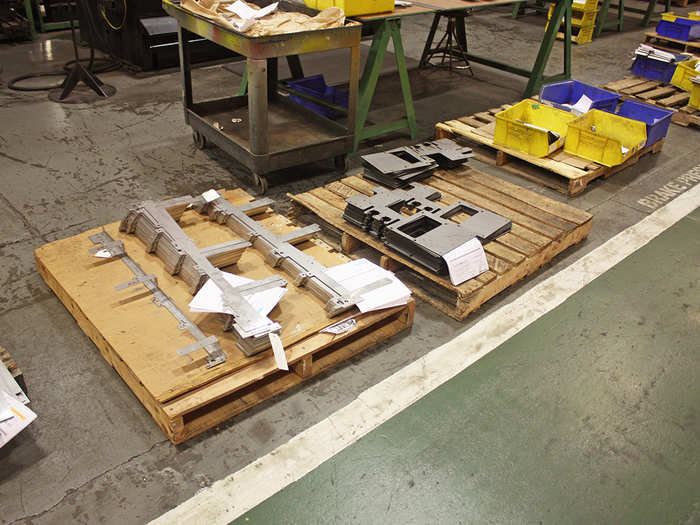
Around 400 people work at the factory, fabricating parts, assembling the cars, running system tests, and overhauling older cars. They also create tools that aid in the manufacturing.
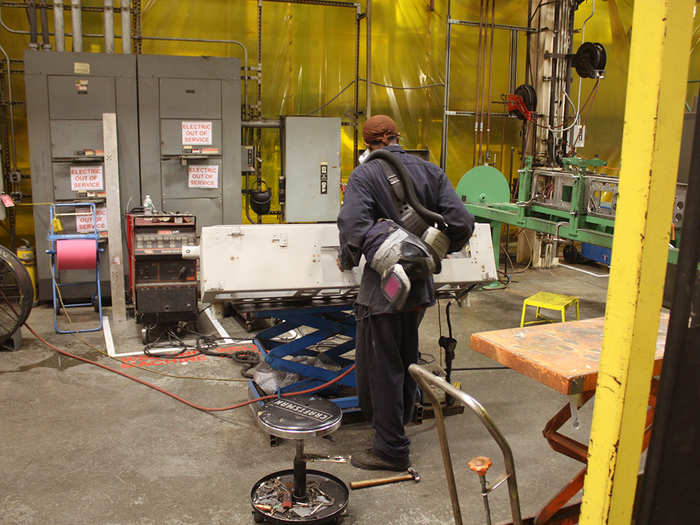
The main bodies of the subway cars, known as "shells," arrive at the Yonkers plant on large flatbed trucks from Kawasaki's plant in Lincoln, Nebraska.
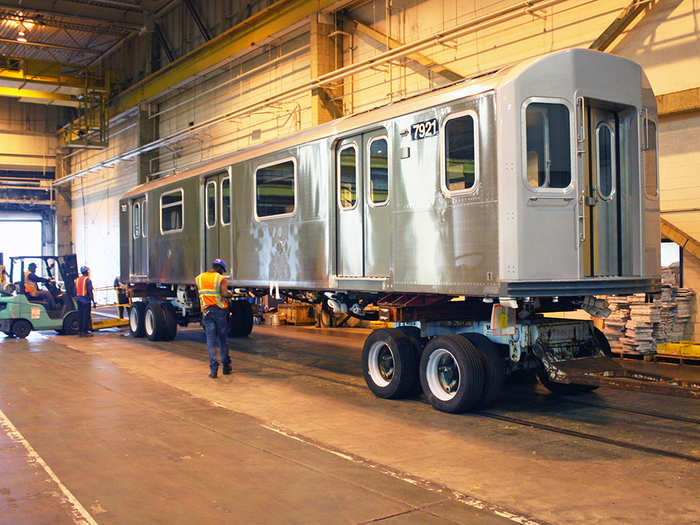
Other cars which have been in use and are in need of refurbishing are sent to the factory as well.
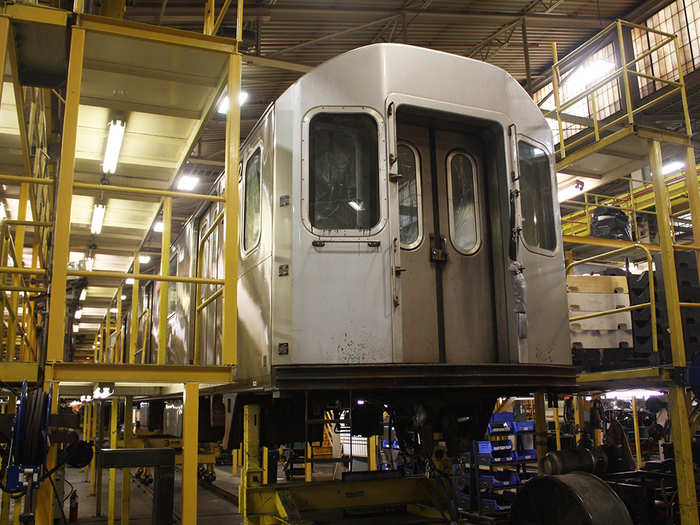
When they arrive, the cars are placed on a long track in the center of the facility, where they are worked on. You can see that the work platform is two-tiered, allowing workers to install equipment, like air conditioning, in the roof compartment.
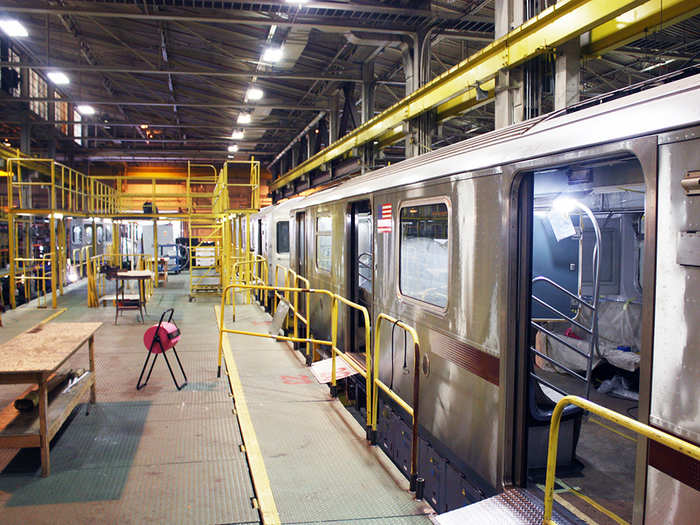
This train looks like it might be used for the L or the F lines.
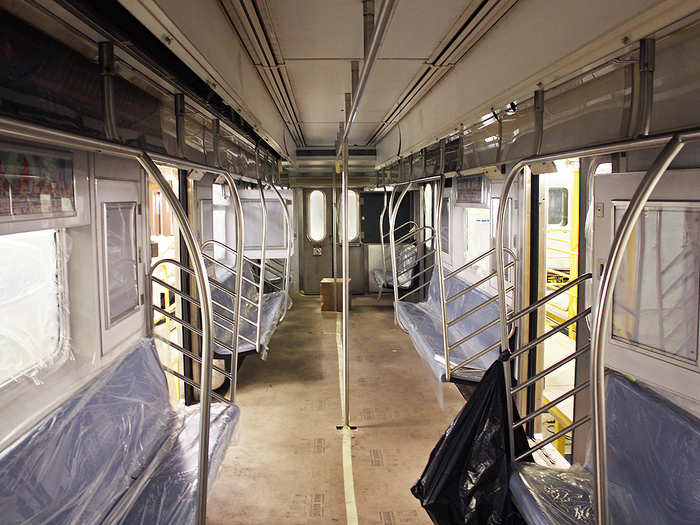
On the lower track, workers place wheels, also called "trucks." Just like the shells, Kawasaki works on both brand-new and refurbished trucks. The wheels are 32 inches in diameter and each truck can weigh around 8.5 tons.
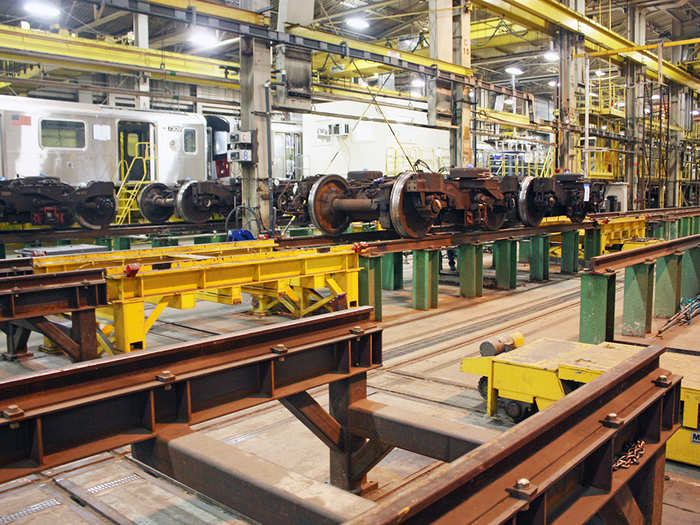
On this refurbished truck, we can see the shoe that connects to the electrified "third rail," giving the truck its power. Each truck is self-propelled using that voltage and also comes with its own airbags.
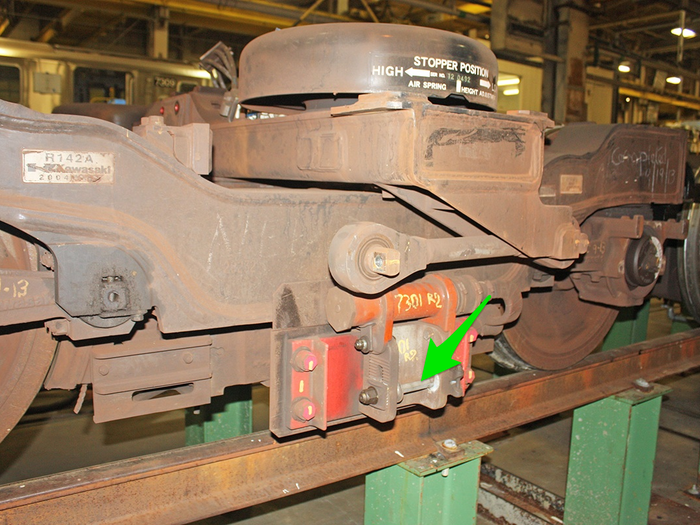
Once both the car and the truck are ready to go, the truck is moved on the lower set of rails, underneath the subway car, and the two are "married."
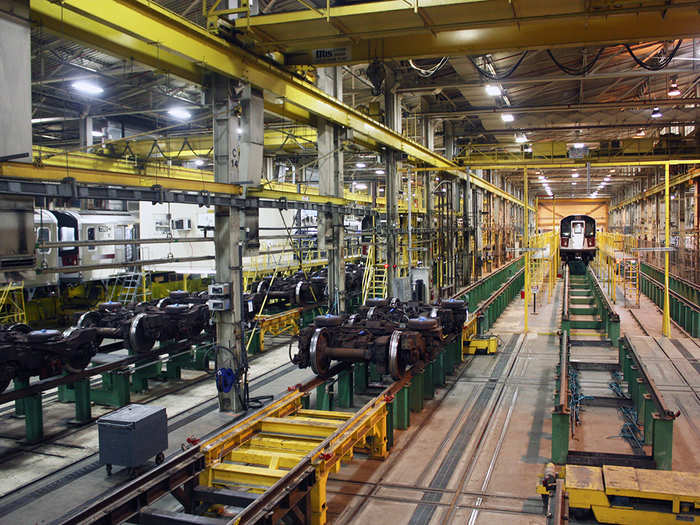
The cars go through rigorous testing at each stage of the building process. This machine runs several tests, including one which simulates the full weight of a subway car completely filled to capacity. During each work contract, a "customer" inspector who is designated and hired by the authorities contracting the work oversees the examinations.
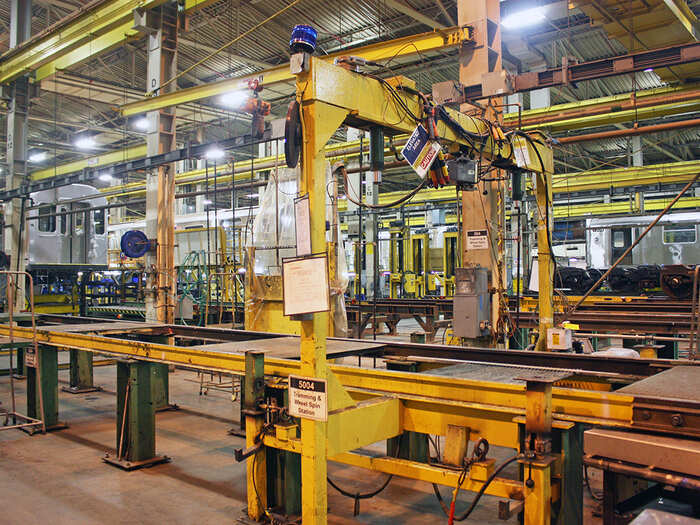
Cars can also be tested outside on the plants short outdoor testing track, mimicking real subway tracks. Note the factory's proximity to the Metro North railway line, which Kawasaki is able to use for transporting new subway cars as well.
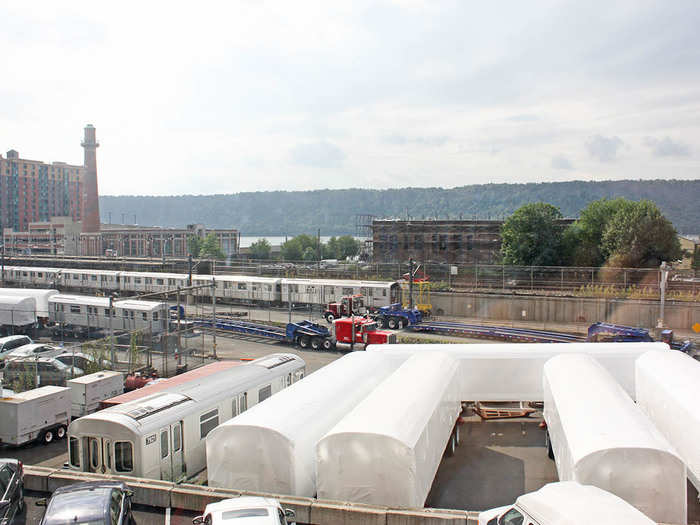
Once a car is complete, it is brought to the end of the track, where two "traverser tables" pick up each truck. The tables are remote-controlled and are used to move the cars to flatbed trucks or to the tracks outside. From there, it's off to the subway system and a long life transporting you all over the city.
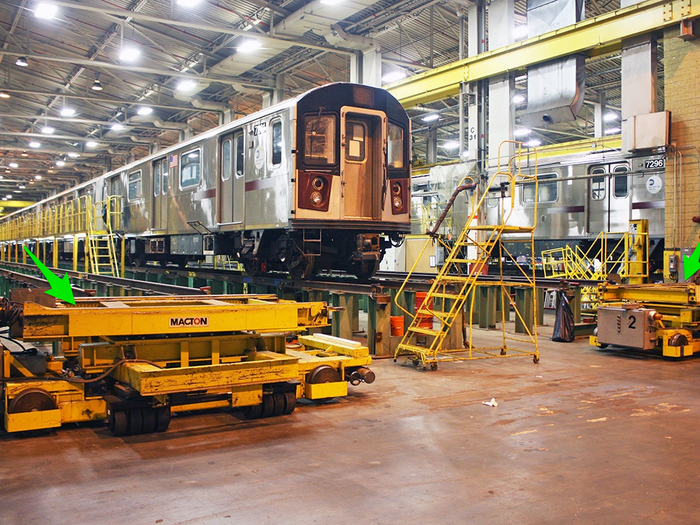
Now want to know where some of the subways cars go once they're retired?
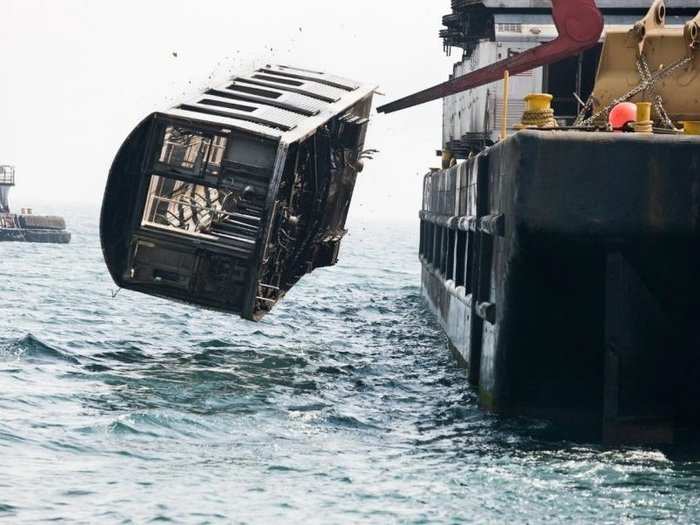
Popular Right Now
Popular Keywords
Advertisement